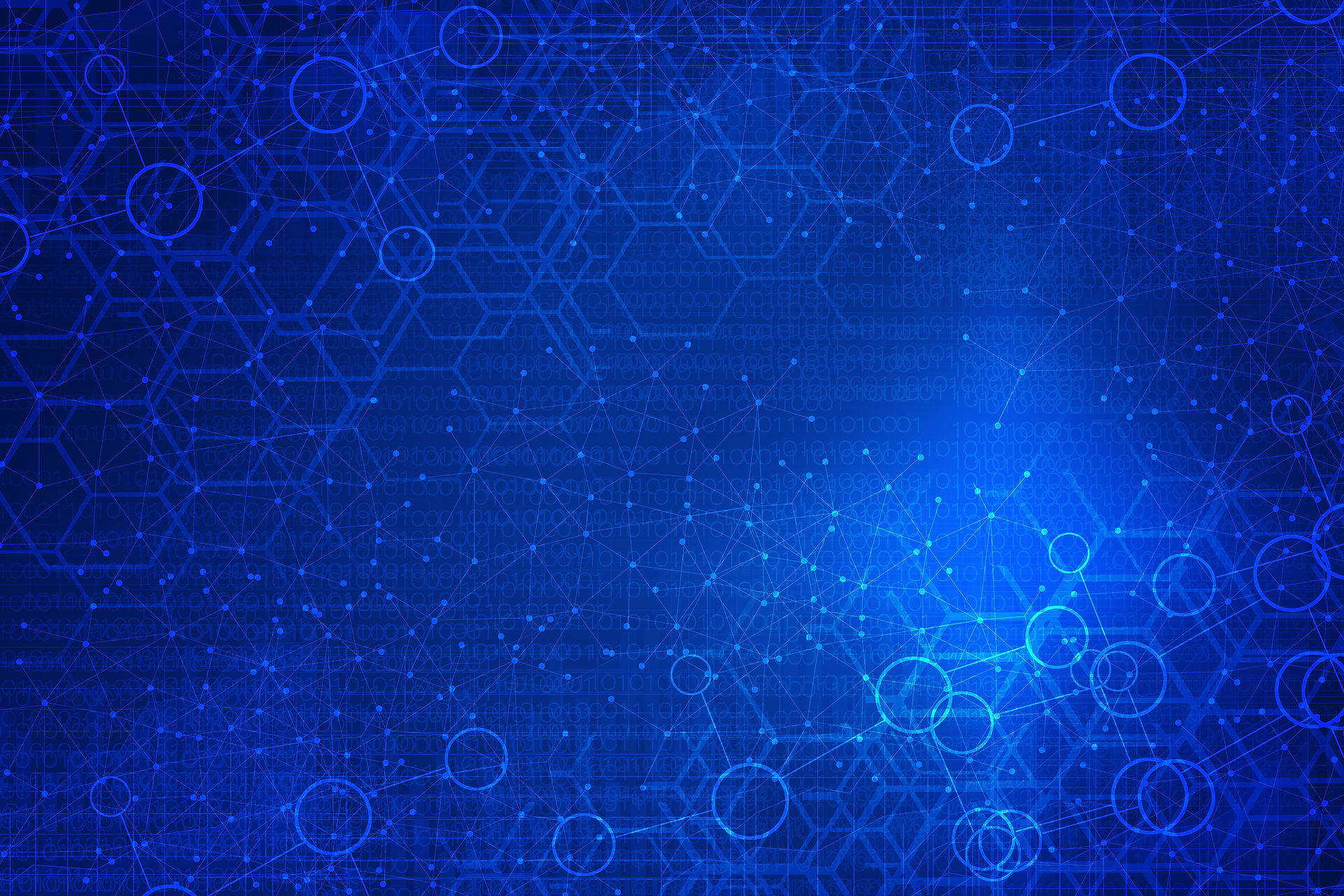

Industrial Internet of Things Appliance
Remove PCs from the factory floor to implement MES.
​The IIoTA™ connects Operational Technology (OT) used in production to Information Technology (IT) used in the office without PCs, so production can "speak" their own controls language to ensure machine availability while the network security of IT remains intact.
OPC:
"Oh Please Connect
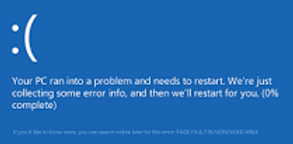
OPC - OLE for Process Control, is PC-based and has unfortunately been accepted as the default technology to transport data.
​
OPC communicates from an IT perspective: regular security patches, large data packets, and slow data rates. Unfortunately, OT is not the same as IT. The data is different. so why try to converge the two?
​
Learn how the IIoTA™ isolates OT from IT and provides a point-and-click data connection.
​

Managers, PCs on the production floor are preventing the acquisition of the machine data (MDA) you need to meet your goals. Engineers responsible for Operational Technology (OT), and IT professionals responsible for system administration cannot take ownership of the PC and middleware used in production because of the natural conflict between the two systems' responsibilities and expertise.
Learn how the IIoTA™ can be used to capitalize on OT's and IT's specialized skills while serving the data that's so badly needed to limit loss in order processing.
QA:
Quality Assurance
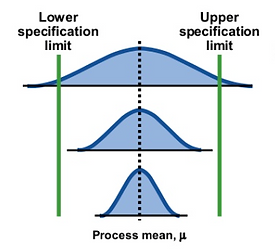
A reliable data connection to the factory floor limits loss by integrating quality management with production management.
​
Production Data Acquisition (PDA) and Machine Data Acquisition (MDA) can be connected directly to a database, without a PC, to communicate with Statistical Process Controls (SPC) to improve QA processes.
​
Learn how the IIoTA's™ event-based triggers and database commands support validation, traceability, and conformity.